This IRG investigate the
behavior of thin film. Many different classes of films are investigated
within the interdisciplinary effort. These include colloidal films,
which are important in their own right as coating materials and which
can be used as model systems for the study of the structures that
can form at the interfaces. These also include films of more traditional
materials, whose properties are being investigated. This work will
continue as the participants begin to unravel the details of the
behavior observed, and apply this to the development of improved
descriptions of the physics.
Drying is a crucial step in the processing of many
forms of thin films, from a common coat of paint to emerging photonic
band-gap structures. As the suspending fluid evaporates, fracture,
delamination, and buckling can occur, ruining the quality of the
thin film. Weitz, Hutchinson and Xie,
working with a series of REU students, explored drying of nanoparticle
suspensions, which are particularly prone to fracture. In the nanoparticle
regime, drying stresses, originating from the affinity of the fluid
for suspended particles, can exceed 1000 times atmospheric pressure.
These enormous stresses can create beautiful patterns of cracks
in drying films. The dynamics of crack growth sheds light on the
subtle interplay of the elasticity of the jammed particle network
with the viscous fluid permeating the pore space. Since these gaps
are only a few molecules across, fluid molecules can be arrested
by strong short-ranged interactions with the nanoparticles. Recently
several MRSEC REU students have demonstrated the importance of
these molecular-scale interactions on the macroscopic dynamics
of drying nanoparticle suspensions, and have determined the means
by which the cracks form as the film dries. These studies will
be extended to investigate the buckling of shells of particles
formed when particle-laden droplets dry.
In another project, Vlassak is
collaborating with Spaepen and Hutchinson to
develop an understanding of the effect of various microstructural
parameters on the mechanical behavior of thin metal films. They
have developed an experimental technique to evaluate the stress-strain
behavior of thin metal films using simple silicon micromachining
techniques. This past year they used this technique for a focused
study of the mechanical behavior of electroplated Cu thin films
with controlled microstructures.
The effect of film thickness was studied
by preparing Cu films with varying thickness but constant microstructure
using chemical mechanical polishing (CMP). Both unpassivated films
and films passivated with 20–50 nm of Ti were investigated.
The constant microstructure was confirmed by measuring the orientation
distribution functions (ODF) of the films by means of XRD and by
measuring the grain size through use of orientation imaging microscopy
(OIM). Discrete dislocation modeling for films on substrates suggests
that when deforming a film on a substrate, a boundary layer with
increased dislocation density forms at the interface with the substrate.
As a result of this boundary layer, the flow stress of the film
increases with decreasing film thickness. To verify formation of
this type of boundary layers, stress-strain curves of both passivated
and unpassivated freestanding films were measured. The passivation
layer has indeed a significant effect on the work hardening rate
of the films. Figure 1 shows the flow stress at
0.4% plastic strain as a function of the thickness of the passivating
layer.
The passivation clearly results in a strengthening of the Cu films
with a maximum effect when the passivating layers are approximately
30 nm thick. This result is consistent with formation of a boundary
layer. TEM observation of deformed films with passivating layers
indeed show a 50–100 nm layer of increased dislocation density
near the Cu/Ti interfaces. The decrease in strengthening for passivating
layers in excess of 30 nm can be attributed to plastic deformation
in the Ti and the resulting decrease in constraint.
Aziz and Golovchenko have
used 3 MeV oxygen irradiation of SiO2 strips to induce large deformations
(Fig. 2). A constitutive relation for this behavior
has been proposed by Hutchinson. With a better
understanding of the ways in which ions produce defects, create
and relieve stress,
and induce mass transport, ion beams might be the basis of morphology
control for the next generation of solid-state electronic and MEMS
devices. MeV ion beams are being used to generate and relieve stresses
in “hard” solids in experiments on morphology evolution
and control. Aziz and Golovchenko are
now using the measured morphology changes for a quantitative test
of theories for morphology evolution. They have also found that
this ion-induced deformation effect can be used to manipulate small
gaps between amorphous metal electrodes, and they have shown that
precise dimensional control is possible using feedback such as
electron tunneling.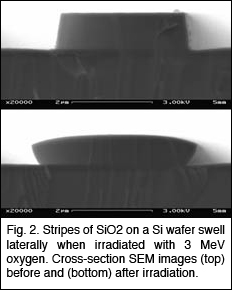
In another project, thin films formed from colloidal
suspensions are used to study a variety of phenomena common to
thin films of more traditional hard materials. The colloidal particles
self-organize into crystalline structures similar to atoms in different
phases of condensed matter. Being several orders of magnitude larger
than atoms, the colloidal particles offer the unique possibility
for studies at convenient length and time scales. Spaepen and Weitz are
performing deformation experiments on thin films of colloidal particles
in the crystalline and amorphous state to gain deeper insight into
atomic processes of plastic deformation. They prepare large fcc colloidal
crystals by slow sedimentation of the colloidal particles onto
a patterned template consisting of holes of particle size in a
coating of PMMA. They find dislocation defects in close analogy
to those in atomic systems. The dislocations that observed are
known as Shockley partial dislocations, the most prominent type
of a dislocation in fcc metals. They constructed a laser
microscope by analogy to a transmission electron microscope: They
apply a two-beam method, in which the strain field of the dislocation
is imaged as a diffraction contrast. The laser microscope enables
them to observe dislocation dynamics during mechanical testing
as well as during crystal growth. They have studied the formation,
motion and interactions of dislocations during indentation tests
as well as during crystal growth on slightly stretched templates.
This is the first use of a laser microscope to image dislocations
in colloidal crystals, and the first attempt to investigate the
dislocations in these crystals. This work will be extended by combining
the imaging using the laser microscope with that obtained using
a confocal microscope, which can image every particle individually,
allowing the defect structure to be precisely determined. In addition,
indentation experiments will be performed to investigate the nucleation
and growth of the defects as the structures are indented.
Hutchinson studied
the buckling of a thin metal film vapor deposited on thick elastomer
substrate.
It develops an equi-biaxial compressive stress state when the system
is cooled due to the large thermal expansion mismatch between the
elastomer and the metal. At a critical stress, the film undergoes
buckling into a family of modes with short wavelengths characteristic
of a thin plate on a compliant elastic foundation. As the system
is further cooled, a highly ordered herringbone pattern has been
observed to develop (Fig. 3). A MRSEC study by Hutchinson has
shown that the herringbone mode constitutes a minimum energy configuration.
A one-dimensional mode (Fig. 3) relaxes compressive
stress perpendicular to the undulations but provides no relief
to the stress in the
film parallel to the undulations. A square checker-board mode provides
relief in all directions, but not nearly as much as the herringbone.
The secret to the herringbone mode is that, apart from local regions
in the vicinity of the “jogs,” the Gaussian curvature
of the film is zero such that there is very little energy penalty
due to stretch.
|