Shape-changing soft material for soft robotics, smart textiles and more
Researchers encode multiple shapes into simple material
By Leah Burrows
December 17, 2024
Liquid crystal elastomers (LCEs) are soft materials that can change shape in response to stimuli such as light or heat—making them promising for applications in soft robotics, wearable and biomedical devices, smart textiles, and more. But, designing compositionally uniform elastomers that can change into different shapes in response to just one stimulus has been challenging and has limited the application of these potentially powerful materials.
Small-molecule liquid crystals (LCs) are a class of compounds capable of self-aligning and forming various self-assembling organized mesophases, which is a phase of matter between a solid and liquid like gelatin, and can be used in broad applications such as displays, controlled drug delivery, and biosensors. By leveraging the LC phase change as the driving force for deformations with the LCEs allows for versatile actuations under stimuli such as heat, light, and humidity, thereby expanding the applicability, and newer applications.
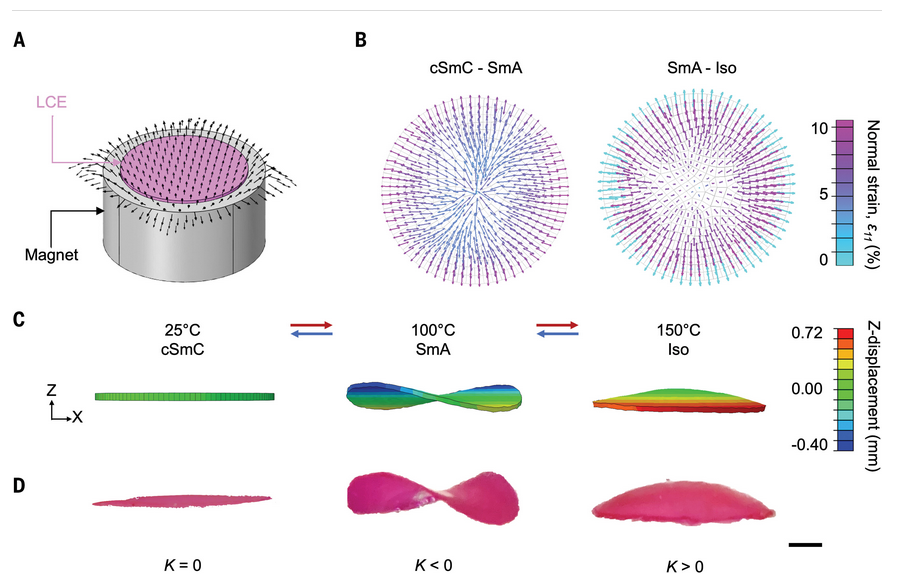
(A) Schematics illustrating the spatial patterning of mesogenic director encoded in a macroscale end-on LCE disk with a magnetic field. (B) Calculated normal strain in the radial direction for an end-on LCE disk upon the cSmC-SmA (left) and the SmA-Iso (right) phase transition. Radial strain is higher along the edges compared with the center during the cSmC-SmA transition and then switches to its lowest along the edges during SmA-Iso transition, indicating a directional change in strain between the two transitions. (C and D) Finite element simulations (C) and experimental results (D) demonstrating the transformation of the initially flat end-on LCE disk (1 cm in diameter × 230 μm thick) into a saddle shape with negative Gaussian curvature and further into a dome shape with positive Gaussian curvature as temperature increases. Pink coloration of LCE films in (D) is caused by doping with rhodamine B for better visualization. Scale bar, 2 mm.
Now, researchers from the Harvard John A. Paulson School of Engineering and Applied Sciences (SEAS) have developed a way to program LCEs with the ability to deform in opposite directions just by heating—opening up a range of applications.
The research was published in Science.
"We have shown that by encoding multiple phase transitions within a single material, we can create scalable, easy to fabricate systems capable of achieving various deformations and shape changes without the need of complex designs or composite materials," said Joanna Aizenberg, the Amy Smith Berylson Professor of Materials Science and Professor of Chemistry & Chemical Biology at SEAS and senior author of the paper.
The team used an approach that combined theoretical modeling, chemical modifications, and mechanics of polymer-polymer interactions to design the system. They began by orienting liquid crystal monomers, which could be bonded together to form polymer chains, along one direction in a magnetic field. The monomers, which were designed with long molecular tails and long linkers, would dangle at the side of polymer chains—like the pendulum of a clock.
When exposed to UV light, the oriented molecules tether together and form polymer chains. The process of polymerization contracts and puts strain on the material, squeezing those aligned monomers into a zig-zag, chevron-like pattern of polymers.
The researchers found that when they increased the temperature, those chevron-shaped polymers flattened and stacked into flat layers. If they increased the temperature further, those layers transformed into a randomly coiled state—like a pile of spaghetti. When they lowered the temperature back down, the random polymers reformed into flat layers then back into chevrons.
"With soft actuators, we need deformations to be reversible so we can cycle them many, many times," said Milan Wilborn, a PhD candidate in Aizenberg's lab and co-first author of the paper. "And we demonstrated that we can switch between these three phases at high frequency, moving quickly between each deformation state."
The researchers also demonstrated that by aligning the molecules in different directions before polymerization, they could encode different shape changes into the material, including flat sheets that move like the fins of stingrays and jellyfish by morphing into saddles and domes.
"What is so powerful about this research is we have this single, soft material which can achieve opposite deformations. So at room temperature, the material is flat, then it forms a saddle when the polymers are stacked in flat layers and then transforms into a dome when the polymers become random," said Wilborn. "We're really excited about using these materials as soft actuators for bioinspired motions."
These transformations respond to not only temperature, but also light and solvent, making them useful for applications from smart textiles to temperature-regulating robotic skins.
Authorship, funding, disclosures
This research was co-authored by Yuxing Yao, Baptiste Lemaire, Foteini Trigka, Friedrich Stricker, Alan H. Weible, Shucong Li, Robert K. A. Bennett, Tung Chun Cheung, Alison Grinthal, Mikhail Zhernenkov, Guillaume Freychet, Patryk Wąsik, Boris Kozinsky, Michael M. Lerch, and Xiaoguang Wang.
The research was supported by the US Department of Energy, Office of Science, Basic Energy Sciences; and the National Science Foundation through the Harvard University Materials Research Science and Engineering Center grant DMR-2011754.